Needed a solution to fert dosing whilst I am away for 3 weeks shortly (and as I keep forgetting). Time to make a gadget....
Here is the finished item, awaiting to be fitted.

And two one litre containers for the mixes.

And inside.
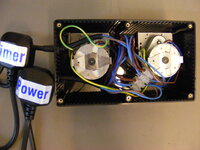
I got two peristaltic pumps from http://www.williamson-shop.co.uk/ for £42 each. Part number 101.015.230.030/4. 3rpm 4 roller (no back flow valve needed) giving about 3ml per minute. Also 5m of 4mm PVC pipe.
Case part number 493-5786 from RS. Didn't want to get from RS (as might be trade only) but Maplin near me had zero stock of anything remotely useful.
Switches 394-475 from RS. Any mains rated double pole double throw switch will do.
Two computer IEC mains leads with IEC plug chopped off. Grommit & cable tie for cable.
Suitable mains rated blue, brown and earth wire for internal wiring.
Heatshrink and chocolate block.
The connections for the switches are soldered and sleeved with heat shrink. The metal of the pumps is connected to earth from both leads.
Here is the wiring diagram.
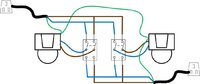
Operation
The the switches allow either pump to be connected to either mains lead.
Normally (in my case) the switches wil be down, selecting the "timer" mains lead, plugged into my timer. I will have timer set for 3 minutes every 24hours to give approx 9ml macro and micro.
To prime the pumps, which considering their small capacity will take a while, push the switches up which connects them to the "power" mains lead. Once primed switch back to "timer"...job done.
Also allows each pump to be run individually, one off each mains lead, if in the future I decide to dose say macro every two days interleaved with a different sized micro every two days.
Made this tube holder out of a 32mm solvent weld 90 bend with a 14mm cut out. Plastic nut and bolts and couple of P-clips to hold tubes in place and prevent tube falling out.
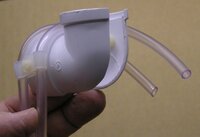
Well here it is, wires out from back of box, both solutions piped in and back made for shelf to prevent the bottles falling out the back. Plenty of cable ties to hold pipes together and clamp pipes onto pump barbs. Also remember to drill a 1mm hole in bottle cap to allow air in. Takes ages to prime the pumps as 3ml/minute is not a lot and the pipe contains quite a volume of liquid in 1 metre odd. They also prime at different times due to different pipe length, so ability to have individual manual prime is handy.
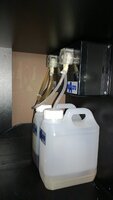
Here is what the outlet pipes look like 22 hours after last pump, absolutely no sign of it running back which has been a problem many people have encountered using cheaper 2 roller peristatic pumps..
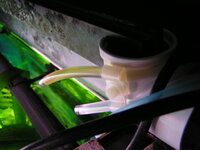
I spent a while pumping water to "calibrate" the system and found I got about 30ml in 10 minutes, which matches the pump specification exactly (3ml per minute).
My tank is 180l (say call 200l) and EI dosing is 10ml per 50l every other day, which is 40ml dose. Thus is 20ml a day.
Thus to pump 20ml @ 3ml/minute I would need 6-7 minutes run time. As set on my Home Easy remote control, dosing couple of minute before lights off in the evening.
-------------------------------UPDATE BELOW -----------------------------------
Well here is an update with an alternate relay switching circuit that alternately switches power between the two pumps. When power is first applied it runs one pump and when power is next applied (next day for EI dosing) it runs the other pump. This means a single timer (& mains lead) may be used to alternately dose macro and micro.
Below is the circuit I used.

And wired up to mains & pumps as below.
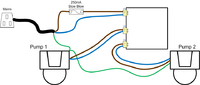
My version of the circuit made on some veroboard.

The circuit is based around latching relay RL1, the state of contacts RL1C and RL1D being set or reset by coils RL1A and RL1B. As it is a latching relay it remembers its state over power cycles. Contacts RL1D are used to switch the mains to P2 or P3 connected to the macro and micro peristaltic pumps.
Mains, from time switch, is connected via P1 to 12V transformer T1. P1 is supplied from the mains via a 250mA slow blow fuse. The 12V AC (actually about 15V as circuit doesn't really load the transformer that much) is rectified to DC via D1-D4 and smoothed by C1. Note C1 is purposely a small value as we don't require 100% smooth DC and also require the DC go away reasonably quickly once the mains is turned off.
Once RL2 has sufficient voltage across the coil, its contacts RL2B and RL2B close connecting C2 or C3, via latching relay contact RL1C to the supply via D5 and current limiting resistor R1. Thus either C2 or C3 will get charged depending on the latched state of RL1C.
When mains power is removed, by the time switch, the voltage across C1 quickly falls and relay RL2 opens, connecting the now charged C2 or C3 across the latching relay set (RL1A) or reset (RL1B) coils. Thus the capacitor discharges through the coil and switches over the latching relay, ready for when power is applied next via the time switch. D5 is necessary to stop C2 or C3 being discharged when the power is turned off.
D6, D7 & D8 prevent and back EMF from the relay coils. They are not strictly necessary in this simple application as there are no delicate semiconductor devices that need protecting, but will provide an element of relay contact protection.
The capacitors are generously over rated at 35V and 105C temperature, so should last millions of hours, epecially as they are only likely to be powered on for couple of minutes every 24hours. The LED's are not strictly necessary, but are/were handy to indicate the latched relay position whilst I built the circuit and tested it on a 12V power supply, rather than mains 240V. They can be just seen in my photo. In the finished box I connected the LED's to long wires and mounted them on the front of the box (where my original switches were). LED's, if used, must be 2mA low current LED's so as to not discharge C2 or C3 before they are applied to the relay coils.
Below is the parts list. I got parts from RS (http://rswww.com) and Maplin (http://www.maplin.com) as both are near me in Southampton. RS also have the datasheets for the relay pin outs as well.

When making, be careful as mains is being used, make sure a slow blow fuse is fitted. I removed all the underside copper tracking, where not used, on the mains connectivity bit, using a 4mm twist drill (by hand).
I managed to mount the board in the bottom of the box, it was a bit tight as the transformer is quite large and rather limits the board placement between one of the pumps and reinforcing pillar in the box.
If I was making it again I would make it on a much larger piece of board so I wouldn't have to cram all the components in and not have to have some on the underside of the board.
And if I was making it again again I would use a simple microcontroller and single relay, and might be able to do away with mains transformer and do it all in the microcontroller software, but as I am not an expert on microcontrollers will leave for another day. 😀
Been using for a week or two now, works fine. Enjoy. 😀
Here is the finished item, awaiting to be fitted.

And two one litre containers for the mixes.

And inside.
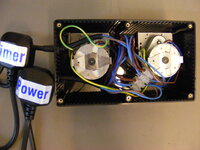
I got two peristaltic pumps from http://www.williamson-shop.co.uk/ for £42 each. Part number 101.015.230.030/4. 3rpm 4 roller (no back flow valve needed) giving about 3ml per minute. Also 5m of 4mm PVC pipe.
Case part number 493-5786 from RS. Didn't want to get from RS (as might be trade only) but Maplin near me had zero stock of anything remotely useful.
Switches 394-475 from RS. Any mains rated double pole double throw switch will do.
Two computer IEC mains leads with IEC plug chopped off. Grommit & cable tie for cable.
Suitable mains rated blue, brown and earth wire for internal wiring.
Heatshrink and chocolate block.
The connections for the switches are soldered and sleeved with heat shrink. The metal of the pumps is connected to earth from both leads.
Here is the wiring diagram.
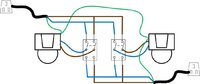
Operation
The the switches allow either pump to be connected to either mains lead.
Normally (in my case) the switches wil be down, selecting the "timer" mains lead, plugged into my timer. I will have timer set for 3 minutes every 24hours to give approx 9ml macro and micro.
To prime the pumps, which considering their small capacity will take a while, push the switches up which connects them to the "power" mains lead. Once primed switch back to "timer"...job done.
Also allows each pump to be run individually, one off each mains lead, if in the future I decide to dose say macro every two days interleaved with a different sized micro every two days.
Made this tube holder out of a 32mm solvent weld 90 bend with a 14mm cut out. Plastic nut and bolts and couple of P-clips to hold tubes in place and prevent tube falling out.
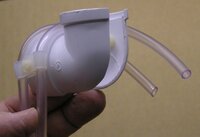
Well here it is, wires out from back of box, both solutions piped in and back made for shelf to prevent the bottles falling out the back. Plenty of cable ties to hold pipes together and clamp pipes onto pump barbs. Also remember to drill a 1mm hole in bottle cap to allow air in. Takes ages to prime the pumps as 3ml/minute is not a lot and the pipe contains quite a volume of liquid in 1 metre odd. They also prime at different times due to different pipe length, so ability to have individual manual prime is handy.
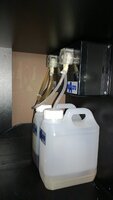
Here is what the outlet pipes look like 22 hours after last pump, absolutely no sign of it running back which has been a problem many people have encountered using cheaper 2 roller peristatic pumps..
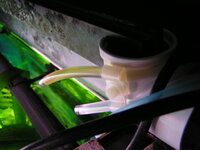
I spent a while pumping water to "calibrate" the system and found I got about 30ml in 10 minutes, which matches the pump specification exactly (3ml per minute).
My tank is 180l (say call 200l) and EI dosing is 10ml per 50l every other day, which is 40ml dose. Thus is 20ml a day.
Thus to pump 20ml @ 3ml/minute I would need 6-7 minutes run time. As set on my Home Easy remote control, dosing couple of minute before lights off in the evening.
-------------------------------UPDATE BELOW -----------------------------------
Well here is an update with an alternate relay switching circuit that alternately switches power between the two pumps. When power is first applied it runs one pump and when power is next applied (next day for EI dosing) it runs the other pump. This means a single timer (& mains lead) may be used to alternately dose macro and micro.
Below is the circuit I used.

And wired up to mains & pumps as below.
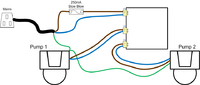
My version of the circuit made on some veroboard.

The circuit is based around latching relay RL1, the state of contacts RL1C and RL1D being set or reset by coils RL1A and RL1B. As it is a latching relay it remembers its state over power cycles. Contacts RL1D are used to switch the mains to P2 or P3 connected to the macro and micro peristaltic pumps.
Mains, from time switch, is connected via P1 to 12V transformer T1. P1 is supplied from the mains via a 250mA slow blow fuse. The 12V AC (actually about 15V as circuit doesn't really load the transformer that much) is rectified to DC via D1-D4 and smoothed by C1. Note C1 is purposely a small value as we don't require 100% smooth DC and also require the DC go away reasonably quickly once the mains is turned off.
Once RL2 has sufficient voltage across the coil, its contacts RL2B and RL2B close connecting C2 or C3, via latching relay contact RL1C to the supply via D5 and current limiting resistor R1. Thus either C2 or C3 will get charged depending on the latched state of RL1C.
When mains power is removed, by the time switch, the voltage across C1 quickly falls and relay RL2 opens, connecting the now charged C2 or C3 across the latching relay set (RL1A) or reset (RL1B) coils. Thus the capacitor discharges through the coil and switches over the latching relay, ready for when power is applied next via the time switch. D5 is necessary to stop C2 or C3 being discharged when the power is turned off.
D6, D7 & D8 prevent and back EMF from the relay coils. They are not strictly necessary in this simple application as there are no delicate semiconductor devices that need protecting, but will provide an element of relay contact protection.
The capacitors are generously over rated at 35V and 105C temperature, so should last millions of hours, epecially as they are only likely to be powered on for couple of minutes every 24hours. The LED's are not strictly necessary, but are/were handy to indicate the latched relay position whilst I built the circuit and tested it on a 12V power supply, rather than mains 240V. They can be just seen in my photo. In the finished box I connected the LED's to long wires and mounted them on the front of the box (where my original switches were). LED's, if used, must be 2mA low current LED's so as to not discharge C2 or C3 before they are applied to the relay coils.
Below is the parts list. I got parts from RS (http://rswww.com) and Maplin (http://www.maplin.com) as both are near me in Southampton. RS also have the datasheets for the relay pin outs as well.

When making, be careful as mains is being used, make sure a slow blow fuse is fitted. I removed all the underside copper tracking, where not used, on the mains connectivity bit, using a 4mm twist drill (by hand).
I managed to mount the board in the bottom of the box, it was a bit tight as the transformer is quite large and rather limits the board placement between one of the pumps and reinforcing pillar in the box.
If I was making it again I would make it on a much larger piece of board so I wouldn't have to cram all the components in and not have to have some on the underside of the board.
And if I was making it again again I would use a simple microcontroller and single relay, and might be able to do away with mains transformer and do it all in the microcontroller software, but as I am not an expert on microcontrollers will leave for another day. 😀
Been using for a week or two now, works fine. Enjoy. 😀
Last edited: